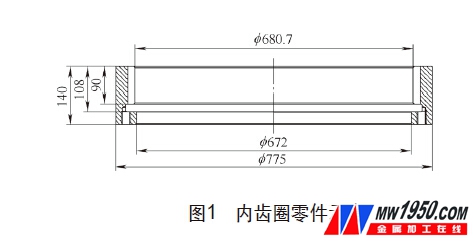
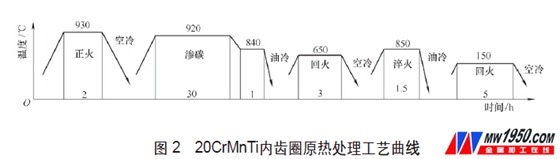
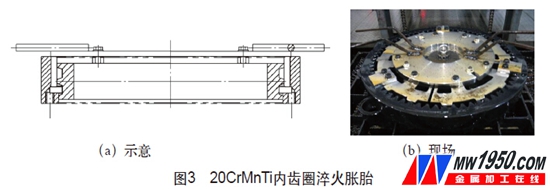
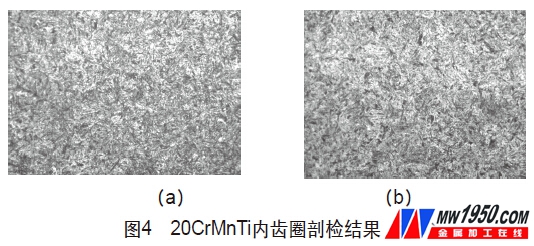
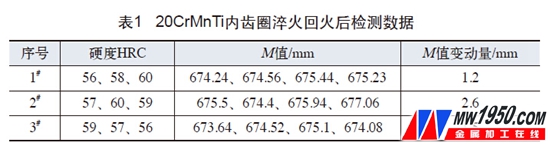
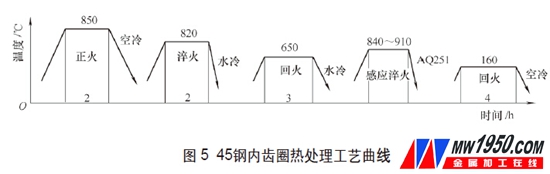
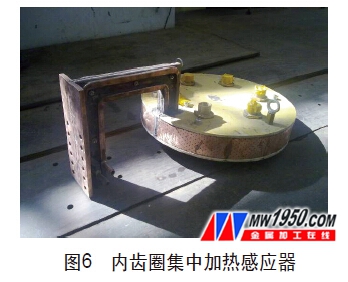
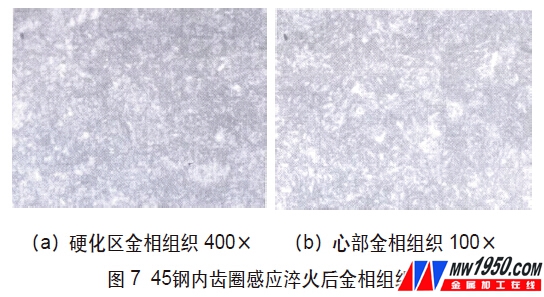
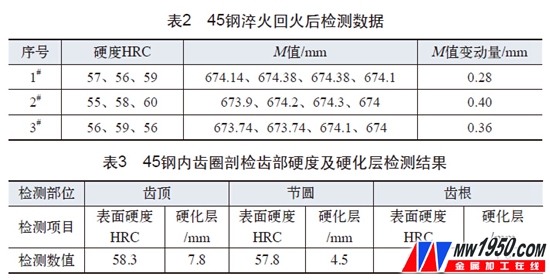
Ethylene amines refers to the acyclic ethylenediamine polymer products, as an important fine chemical intermediates, ethylene amines in organic synthesis, medicine, dye, pesticide, chemical fertilizer, rubber plastic additives, organic solvents and Epoxy Resin Curing Agent, and other fields has been widely used. which become to be one of the fine petrochemical intermediates for the development of China. Ethylenediamine (EDA) is a very important intermediate, mainly used to produce EDTA(chelating agent) and TAEDA(bleach activator), can also be used to produce Organic Dye, Dye-fixing Agent, coating, pesticide, etc. Piperazine can be used to produce anhydrous piperazine, n-methyl piperazine, n-ethyl piperazine, pharmaceutical intermediates, fluperacid, halogen free flame retardant, triethylene diamine. Piperazine has been exported to India and Japan.
Ethylene Amine,Epoxy Resin Curing Agent,Organic Synthesis Intermediates,Chlorinated Polyethylene
NINGBO LUCKY CHEMICAL INDUSTRY CO. LTD , https://www.chinaluckychem.com