Through the repair results of several traditional welding repair processes on the defects of machine tool table castings, the reasons for the poor repair results of machine tool castings are analyzed. The machine tool castings are analyzed by repairing the defects of several traditional welding repair processes on the machine tool table castings. The reason for the poor repair results. Through the research on the repair results of the casting defect repairing machine in the machine tool casting, a new technology and its process for repairing the machine tool castings are determined.
1, welding repair results and analysis of traditional welding repair process
Material HT200, the area of ​​the guide rail defect is S<1000mm2, depth h<8mm. Heat treatment state: 3 pieces are not surface hardened, 1 piece has been surface quenched. Nickel base solder powder F103, cast iron electrode for arc welding: Z308, Z248. 2.1 .2 spray welding equipment, arc welding equipment, nickel-based solder powder F103 (C ≤ 0.15 8.0 < Cr < 12 2.5 < Si < 4.5 1.0 < B < 1.7 Fe ≤ 8 remaining Ni), cast iron electrode: Z308, Z248.
1.1 Spray welding is carried out according to the spray welding process, preheating the rail surface to above 150 °C, after the initial welding powder is sprayed, the spray surface is heated to above 900 °C-1200 °C, so that the solder powder melts to form a flat surface. The heat and heating time are long, the heat receiving area of ​​the workpiece is large, the thermal stress is large, and the crack is more likely to occur than the arc welding, and the crack tends to be larger due to the line shrinkage. The crack tends to be affected by the welding time, the thickness of the spray layer, and the like. The size is limited, and the defects of the weld repair need to be cleaned. Due to the high proportion of Fe in the dust spray, the sprayed layer formed is more similar to the color of the base metal than the base metal. However, due to a certain amount of Ni, it cannot be It is closer to the color of the base metal and can be machined after welding.
1.2 Results Analysis Traditional spray welding, arc welding process, cracks are easy to occur after welding, the workpiece is susceptible to thermal deformation, and secondary pores are prone to occur. The difference between metal color and base metal at weld repair is common. This is also the traditional welding. The repair process cannot completely solve the root cause of machine tool guide defect repair.
1.3 Arc welding with cast iron welding rod Z248 for welding repair, welding repair process is divided into two, the first: pre-heating to 550 ° C-650 ° C before welding, 5-8 hours after welding repair; second: before the workpiece welding Preheating, post-weld insulation for 3-4 hours. Both methods are prone to cracks, hard spots, and it is not easy to machine after welding. The welding rod is cheap. Welding with nickel-based cast iron welding rod Z308 welding rod, welding layer and welding layer The cooling should be stopped until the temperature is below 60 °C. There are few pores in the welding area, cracks are generated, the mechanical processing property is good, the bonding strength is high, and there is no falling off. Due to the influence of the oil absorption and the welding rod blowing force after the machine tool guide is processed, the undercut is easy to occur. Forming "welding traces", the color of the weld repair zone is very different from that of the base metal, and the electrode is expensive.
2, repair effect and analysis of casting defect repair glue:
At present, there are many kinds of filling materials used in enterprises, and the quality is also very different. This paper only based on the experimental results of filling materials that can meet the requirements of casting quality standards (using AK01-2 and AK01- in the Oke brand casting defect repairing glue) 2B two models).
2.1, surface treatment before sizing:
Two unprocessed HT250 test blocks (100X100 X50) have ¢2-¢10mm pores on the surface, several sand holes; two processed HT250 test blocks (100X100X50), surface roughness of 3.2, ¢2-¢10mm Some of the pores of the sand hole. First use a power tool or a spatula to remove sand and scale, and then clean the surface with acetone.
2.2, adjusting and coating:
For the filling of defects on the unprocessed surface, the non-machined surface defect repairing adhesive (AK01-2) should be used. Take 2 parts of A glue and 1 part of B glue according to the weight ratio of 2:1, and mix well (mix in one direction) ) Use a special rubber knife or hard rubber to scrape the rubber forcefully. Pay attention to the air in the hole. The glue should be used within 30-40 minutes. If the defect of the machined surface is filled, the surface defect repair glue should be selected (AK01). -2B) Adjust the A and B colloids according to the specified ratio in the manual. During the gluing process, attention should be paid to the surface leveling and the protection of the datum.
2.3, effect detection and analysis:
After 12 hours, the unprocessed test piece was shot blasted, no peeling occurred, and the surface state and color were close to the reference surface. After 12 hours, the processed test piece was re-turned and milled, no peeling, color and processing were observed. The surface is close.
2.4, Conclusion:
The tested rubber can meet the requirements of shot blasting, sand blasting, car, milling, boring and grinding without falling off, which can meet the repairing requirements of performance; the color is close to the base surface, and can not meet the strict chromatic aberration requirements. The colloid is non-metallic. It needs to be recognized by customers, but the repair cost is low, easy to use, high efficiency, and it has gradually become a wide-ranging repair method.
3, welding repair effect and analysis of casting defect repair machine:
3.1 Preparation and analysis of the test bar Prepare a test bar of Φ30mm×200mm, the material is HT250, the surface roughness is Ra0.8, drill 4-5 holes of Φ5mm depth 3-4mm on the surface, cast with AKZQB-2000C type The defect repairing machine is welded, the material is 0.8#, the metal piece with the thickness of 0.25mm and the HT250 iron wire with the thickness of 0.4mm. There is no obvious boundary line at the weld repair, the transition area is small, and no carbonization is seen near the weld repair point. When the material precipitates, the metal structure of the weld repair is dense, and no crack is generated. Near the weld repair point and the whole test bar, the metal color of the weld repair point is the same as that of the base metal, and the weld fill point of 0.8# is denser than the base metal. The welding material of the same material has the same density as the base material. The metallographic structure analysis: no crack, the surrounding metallographic structure has not changed, no internal stress, no hardening, softening phenomenon.
3.2 Welding repair effect and analysis of guide rail defects
Material: HT200; heat treatment state: surface quenching 2 pieces, hardness 50-56HRC; no surface quenching 2 pieces, hardness 170-230HB, defect Φ1-Φ6mm; depth 3-4mm defects several. AKZQB-2000C type casting defect repairing machine , the material is 0.8#, Φ0.8mm wire and iron scrap of HT200 material.
Welding repair effect and analysis: macroscopic inspection, the metal color of the welding repair point is the same as that of the base metal, no undercut, no burn marks, near the weld repair point and the whole workpiece at room temperature. The weld repair condition is detected on site with a 30 times magnifying glass and a hardness tester. The results show that there is no obvious dividing line, the welding point metal is dense, no crack, no blisters, 0.8# replenishing welding point hardness 180-220HB, HT200 replenishing point hardness 210-240HB, unquenched rail surface welding repair point Nearby, hardness HB160-210. Hardness near the repair point of quenching guide rail 51-56HRC, no annealing, softening phenomenon, qualified by the detection agent. Can be machined, the metal color of the weld repair is the same as the base metal, to meet the defects of the processing surface Repair quality inspection requirements.
4 Conclusion:
4.1 The traditional spray welding, arc welding and other processes have certain limitations on the defect repair of castings. The sprayable weldability is good, but it is prone to cracks, thermal deformation, annealing, etc. The color and the mother are greatly different. Mechanical combination, the combined strength is lower than that of arc welding. The welding repair effect of arc welding is directly related to the selection of welding rod. The processability of Z308 and the non-production of crack are good, but the difference between welding trace and color and the matrix is ​​difficult to eliminate. And the price is high. The pre-weld heating of the castings in the traditional welding repair process and the post-weld insulation also cause certain inconvenience to the welding repair of the large castings. The casting defect repairing glue is convenient to use, low in price and high in efficiency, but belongs to non-metal. The color can not be completely consistent, it is not suitable for castings with strict color requirements.
4.2 Using the casting defect repairing machine to repair the defects of the casting parts, the castings do not heat up during the repair process, no deformation, no cracks occur, the welding points are dense, no hard spots, no annealing, any machining can be carried out. The choice of the material is not restricted by the material. Through the choice of different material materials, the performance of the welding point can be achieved, and the color and the matrix are unified. The material of the material and the matrix are metallurgical, and the bonding strength is high, and no off welding occurs. The quality is in line with the quality inspection standard of casting products, and it is a new technology that is worthy of widespread promotion. However, the welding repair range of casting defect repairing machine is the process of repeated melting and stacking of Φ1.5-Φ1.2mm welding repair points, in large area defects. In the repair process, the repair efficiency is the only factor that restricts its widespread application. For large defects, the composite application of traditional welding repair process and casting defect repairing machine is recommended. http://news.chinawj.com.cn
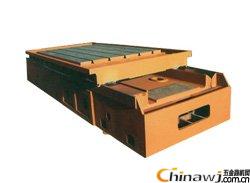
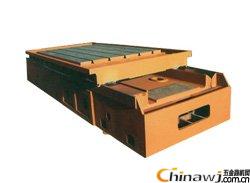
SPAR120
Solid-phase synthesis, as the key process in the production of Bio-pharmaceuticals, is widely used for the synthesis of deoxyribonucleic acid (DNA), peptides, and so on. The synthesis method is to bound the functional group such as methyl, aminomethyl on a bead, which primiarly is polystyrene microsphere with low crosslink. By the benefits of the monodisperse characteristic, the beads have same particle size and crosslink degree with each other, to ensure the consistent swelling properties.
Resins For Solid Phase Synthesis Spar120
Resins For Solid Phase Synthesis Spar120,Alternative Am Resin,Monodisperse Resins For Solid Phase Synthesis,Spar120 Solid-Phase Synthetic Resin
Nanjing Genshine Bio-technology Co., Ltd , http://www.genshine-bio.com